Ceramic capacitors are widely used in electronic devices due to their high reliability, stability, and low cost. They are essential components in various applications, including power supplies, signal filtering, and decoupling. To ensure the quality and performance of ceramic capacitors, there are specific product standards that manufacturers must adhere to. In this article, we will discuss the product standards for ceramic capacitors and their importance in the electronics industry.
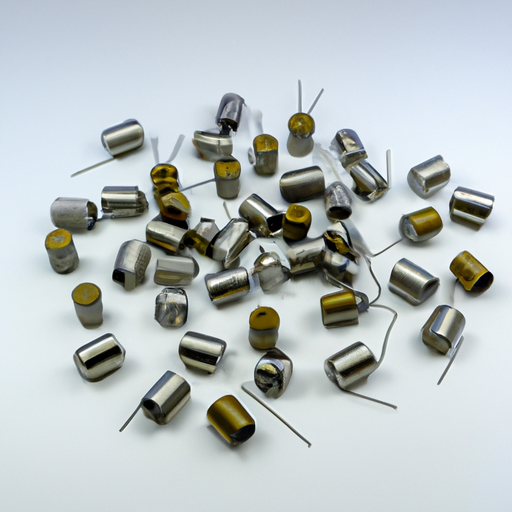
One of the key product standards for ceramic capacitors is the IEC 60384 series, which covers fixed capacitors for use in electronic equipment. This standard specifies the general requirements for ceramic capacitors, including their dimensions, materials, electrical characteristics, and testing methods. It also defines the classification of ceramic capacitors based on their dielectric materials, temperature coefficients, and voltage ratings.
Another important product standard for ceramic capacitors is the EIA-198 series, which provides guidelines for the selection and application of ceramic capacitors in electronic circuits. This standard includes information on the different types of ceramic capacitors, such as multilayer ceramic capacitors (MLCCs), single-layer ceramic capacitors, and ceramic disc capacitors. It also outlines the recommended operating conditions, soldering techniques, and storage requirements for ceramic capacitors.
In addition to these general product standards, there are specific standards for ceramic capacitors used in high-reliability applications, such as military and aerospace systems. These standards, such as MIL-PRF-123 and MIL-PRF-55681, define the additional requirements for ceramic capacitors in terms of environmental testing, reliability assessment, and quality control procedures. Manufacturers that supply ceramic capacitors for these applications must comply with these stringent standards to ensure the performance and durability of their products.
When it comes to testing ceramic capacitors, there are several key parameters that must be evaluated to ensure their quality and reliability. These parameters include capacitance, voltage rating, temperature coefficient, insulation resistance, and equivalent series resistance (ESR). Capacitance is the most critical parameter for ceramic capacitors, as it determines their ability to store and release electrical energy. Voltage rating indicates the maximum voltage that a capacitor can withstand without breakdown. Temperature coefficient defines how the capacitance of a ceramic capacitor changes with temperature variations. Insulation resistance measures the ability of a capacitor to maintain its electrical isolation over time. ESR is a measure of the internal resistance of a capacitor, which affects its efficiency and performance in high-frequency applications.
To meet the product standards for ceramic capacitors, manufacturers must conduct rigorous testing and quality control procedures throughout the production process. This includes incoming inspection of raw materials, in-process testing of components, and final testing of finished products. Testing methods for ceramic capacitors may include capacitance measurement, voltage withstand testing, temperature cycling, humidity testing, and vibration testing. Manufacturers must also implement traceability systems to track the production history of each capacitor and ensure compliance with the relevant standards.
In conclusion, product standards for ceramic capacitors play a crucial role in ensuring the quality, reliability, and performance of these essential electronic components. By adhering to these standards, manufacturers can produce ceramic capacitors that meet the requirements of different applications and industries. Customers can also have confidence in the quality of ceramic capacitors knowing that they have been manufactured in accordance with established standards. As technology continues to advance, it is essential for manufacturers to stay updated on the latest product standards and testing methods to meet the evolving demands of the electronics industry.