Title: Advancements in Optical Instrument Manufacturing Processes
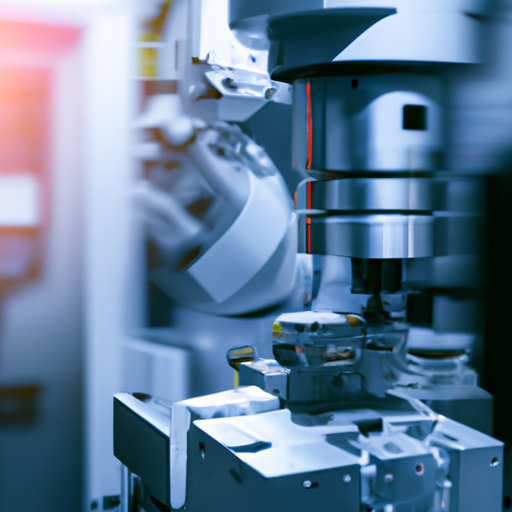
1. Precision Machining: Precision machining plays a crucial role in the manufacturing of optical instruments. Computer Numerical Control (CNC) machines have become increasingly popular due to their ability to produce complex and precise components. CNC machines use computer-aided design (CAD) software to guide the cutting tools, resulting in accurate and repeatable parts. This process ensures the precise alignment of lenses, mirrors, and other optical components, leading to improved optical performance.
2. Diamond Turning: Diamond turning is a specialized manufacturing process used to create precise optical surfaces. It involves using a diamond-tipped cutting tool to shape the material, typically metals or plastics, into the desired form. This process allows for the creation of aspheric lenses, which are essential for correcting aberrations in optical systems. Diamond turning offers high precision, excellent surface finish, and the ability to produce complex shapes, making it ideal for manufacturing optical instruments.
3. Thin Film Coating: Thin film coating is a critical step in optical instrument manufacturing. It involves depositing a thin layer of material onto the surface of optical components to enhance their performance. Various techniques, such as physical vapor deposition (PVD) and chemical vapor deposition (CVD), are used to apply coatings with specific properties, such as anti-reflective, reflective, or protective coatings. Thin film coatings improve light transmission, reduce reflections, and increase durability, thereby enhancing the overall performance of optical instruments.
4. Additive Manufacturing: Additive manufacturing, also known as 3D printing, has gained significant attention in recent years. While traditionally used for prototyping, it is now being explored for the production of optical instruments. Additive manufacturing allows for the creation of complex geometries, reducing the need for assembly and improving overall efficiency. This technique enables the production of customized optical components, reducing costs and lead times. However, challenges such as surface finish and material limitations need to be addressed for widespread adoption in optical instrument manufacturing.
5. Automated Assembly: Automation has transformed various industries, and optical instrument manufacturing is no exception. Automated assembly processes ensure consistent quality, reduce human error, and increase production efficiency. Robots and computer-controlled systems are used to handle delicate optical components, align them accurately, and perform intricate assembly tasks. Automated assembly not only improves productivity but also enhances the reliability and performance of optical instruments.
6. Metrology and Quality Control: Metrology, the science of measurement, plays a crucial role in optical instrument manufacturing. Advanced metrology techniques, such as interferometry and profilometry, are used to measure the shape, surface quality, and optical performance of components. These measurements ensure that the manufactured instruments meet the required specifications. Additionally, automated quality control systems are employed to detect defects, such as scratches or coating imperfections, ensuring the highest level of quality in the final product.
Conclusion: The latest optical instrument manufacturing processes have revolutionized the industry, enabling the production of high-quality, precise, and efficient instruments. Precision machining, diamond turning, thin film coating, additive manufacturing, automated assembly, and advanced metrology techniques have all contributed to the advancement of optical instruments. These processes have improved the performance, reliability, and customization capabilities of optical instruments, benefiting various sectors such as healthcare, telecommunications, and manufacturing. As technology continues to evolve, we can expect further advancements in optical instrument manufacturing, leading to even more innovative and efficient instruments in the future.